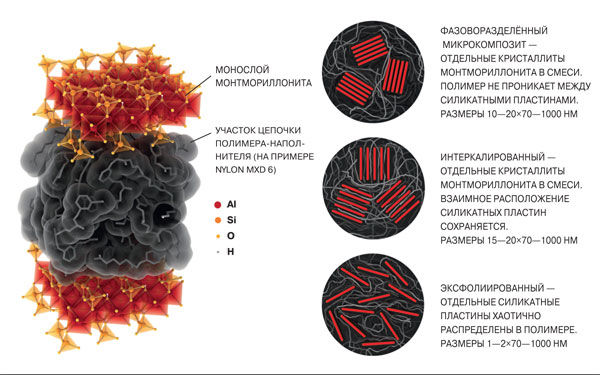
Строение наноструктурированной керамики.
Материалы — основа цивилизации. Недаром даже исторические периоды человечества названы по именам основных технологических материалов — каменный век, бронзовый, железный… И только нынешнее время трудно охарактеризовать каким-то одним материалом. Одно время говорили, что мы живём в эпоху алюминия и титана, потом оказалось, что сейчас эпоха пластмасс, а с развитием электроники мы оказались в веке кремния. Буквально каждый год исследователи и инженеры придумывают что-то новенькое, с необычными, порой фантастическими свойствами. Приведём в качестве примеров пятёрку материалов, появившихся совсем недавно, но претендующих на самое широкое применение.
Начнём с субстанции со странным названием «бронзочугун». Казалось бы, что-нибудь одно: либо чугун, либо бронза. Оказывается — нет, название вполне точное. Чугун —материал не слишком дорогой, доступный, но его механические и антифрикционные свойства от идеала далеки. Бронза, напротив, стоит дорого, зато технологична; её используют в деталях тяжелонагруженных машин и механизмов. Специалистам новосибирского наноцентра «Сигма» удалось совместить положительные качества того и другого. Они ввели в состав чугуна ультрадисперсные частицы тугоплавких металлов и поменяли микрокристаллическую структуру сплава. В результате улучшились его механические и технологические показатели. А введение в чугун меди (в довольно высокой концентрации) сделало материал антифрикционным. Изготовленные из этого сплава втулки успешно прошли испытания на предприятиях в Новосибирске, Абакане и в Магадане, где их тестировали на тяжёлых экскаваторах. Внедрение бронзочугуна даёт ощутимую экономию. «К примеру, для замены всех втулок и опорных катков экскаватора требуется порядка 400 кг бронзочугуна. При стоимости бронзы БрАж 350 руб/кг, а бронзочугуна — 130 руб/кг обновление элементов каждого экскаватора обойдётся почти на 100 тысяч рублей дешевле, при этом прослужат втулки так же долго», — отмечает генеральный директор наноцентра «СИГМА. Новосибирск» Луиза Лесная.
Второй пример. Керамика. Причём не простая, а наноструктурированная. Смысл этого сложного слова в том, что внутреннее строение традиционной керамики носит более или менее случайный характер, а в новых материалах удаётся добиться заранее заданного строения. Это, в свою очередь, даёт возможность проектировать свойства материала.
У керамики есть замечательные свойства: практически абсолютная стойкость к коррозии, высокая износостойкость, стойкость к перепадам температур и высокая теплопроводность. За счёт добавления нанопорошков материал становится очень плотным (снижается его пористость и растёт механическая прочность при сохранении низкого веса изделий).
В рамках совместного с РОСНАНО проекта компания «НЭВЗ-Керамикс» развивает производство сразу нескольких видов таких материалов: керамической брони, износостойкой запорной арматуры для нефтегазовой отрасли и биокерамических протезов для ортопедии и стоматологии.
Бронекерамические блоки и медицинские протезы «НЭВЗ-Керамикс» уже прошли испытания, в ближайшем будущем планируется начать их серийное производство и эффективно заместить импортную продукцию на российском рынке.
Пример третий. Антикоррозионное покрытие. Коррозия — самый страшный и коварный враг всех металлов. По некоторым оценкам, примерно половина всего произведённого в ХХ веке железа уничтожена коррозией. Однако хорошее покрытие зачастую сводит коррозию практически к нулю. Выпуск такого материала освоен портфельной компанией РОСНАНО «Метаклэй» в Карачеве (Брянская область).
Покрытие делают на основе полимерных нанокомпозитов. Наполнителем полимерной матрицы стали наночастицы глины — монтмориллонита. Материал обладает очень низким коэффициентом газопроницаемости и способен работать при температурах от –60 до +80оС. Он особенно эффективен на трубах большого диаметра для магистральных газопроводов. С такой защитой срок службы трубы возрастает до фантастических 60—80 лет. Нанесение нанокомпозита происходит очень быстро — 1 метр трубы диаметром 1420 мм покрывается всего за 30 секунд. Защищённые трубы будут использовать на магистральном газопроводе «Сила Сибири».
Четвёртый пример касается материалов, обеспечивающих чистоту поверхности, подверженной влиянию атмосферных факторов. Защитные гидрофобные покрытия, выпускаемые в нанотехнологическом центре «Дубна» компанией «Защитные покрытия» (а как бы вы её назвали?), придают обработанным поверхностям гидрофобные и олеофобные свойства. То есть с такой поверхности скатываются, не задерживаясь, капли воды и органических жидкостей. Мало того, они увлекают за собой частицы пыли и грязи. В отличие от импортных составов, теряющих свойства при температуре ниже 5оC, дубненские покрытия работают во всём диапазоне температур нашего климата и защищают стёкла не только от дождя, но и от наледи. Важно и то, что на стёклах зданий, в том числе высотных, подверженных влиянию сильных ветров, состав держится более года. А это прямая экономия на мойке окон и освещении помещений. Некоторые официальные автодилеры пользуются составами из Дубны при подготовке к продаже дорогих автомобилей.
И, наконец, пятый пример: антиобледенительные покрытия на основе жидкофазных нанокомпозитов и фторполимеров (ЖНФ). Они обладают одновременно гидрофобными, антифрикционными и противокоррозионными свойствами, то есть универсальны и многофункциональны. Испытания, проведённые в саранской Технологической компании «ЖНФ» (Центр нанотехнологий и наноматериалов Республики Мордовия) доказали впервые в мировой практике очень хороший уровень адгезии при нанесении фторполимеров на металлические поверхности. В исходном виде материал жидкофазный, а потому технология его нанесения оптимизируется и для сложных условий. Покрытие очень перспективно для обработки судов, морских буровых платформ, самолётов, скоростных поездов. Оно препятствует образованию кристаллов льда на поверхности обработанного материала. Состав уже испытали на материалах, используемых в авиации, где проблема обледенения является одной из ключевых.
Кстати, покрытие оказалось весьма эффективным средством против биообрастания на судах и буровых платформах. И, что может показаться совсем уж неожиданным, фрезы для деревообработки, покрытые фторполимерным составом, испытывают меньшее сопротивление в материале, меньше нагреваются в процессе работы и дольше служат.
Комментарии (0)